Have you ever wondered whether your cable hauling ropes are stashed in the best way possible? Are you worried about how exposure to moisture or UV rays might affect their durability? Keeping these ropes in top condition can be trickier than it sounds, especially when you’re juggling multiple tasks on the job site.
Storing cable hauling ropes properly is vital because it adds years to their life and reduces safety risks. If you’ve ever dealt with unexpected rope failures, you know how costly and stressful it can be. By setting up a well-organised storage system, you’re not only cutting down on future replacement costs but also building a safer working environment for everyone.
Understanding Cable Hauling Ropes-
Cable hauling ropes are essential for heavy-duty lifting, pulling, and crane operations on worksites across Australia. Without them, tasks that involve significant loads—such as cable yarding in logging systems or hoisting equipment onto wire rope cranes—would be nearly impossible. While these ropes might look sturdy at a glance, understanding the different types available and the hazards associated with them is key to staying safe.
Types of Cable Used for Hauling
There are several types of cable used for hauling, each chosen for specific tasks. Steel wire ropes are incredibly durable, making them perfect for construction, crane work, and cable logging. Fibre ropes—commonly derived from synthetic materials—serve well in lighter applications but may not stand up to the rigours of heavy loads as effectively. Factors like breaking strength, resistance to bending fatigue, and flexibility all play a role in deciding which cable is ideal for your project. By ensuring the right choice from the start, you lower the chances of premature wear and potential accidents.
Cable Pulling Hazards and Control Measures
Cable pulling hazards and control measures can’t be overlooked if you want to maintain a safe work zone. Many accidents happen when ropes rub against sharp edges, experience sudden loading, or aren’t properly handled during rope installation. To manage these hazards, conduct regular inspections, train your crew on correct pulling methods, and use protective materials to shield cables from metal edges. Minimising friction and ensuring that ropes run smoothly around pulleys can further lower the risk of damage during hauling operations.
Seizing Wire Rope and Seizing Wire Rope Ends Explained
When you seize wire rope ends, you wrap them tightly with seizing wire—usually soft, galvanised wire to hold the rope strands together. This process is particularly helpful for logging and cable hauling operations, where fraying can create serious safety hazards. By securing the rope’s end, you not only preserve the rope’s integrity but also make it easier to handle and store without worrying about sharp strands catching or injuring anyone on site.
Taking the right steps before storing your cable hauling ropes can make a massive difference to their longevity. A quick, careless approach—like tossing them into a damp storeroom—could lead to rust, weakened strands, and reduced wire rope safety. On the other hand, a thorough preparation plan helps keep ropes in top shape, so they’ll be ready when you need them most.
Inspecting for Damage and Wear
Before stowing any rope, carry out a detailed inspection. Look for broken strands, worn sections, or signs of corrosion. Rust spots might be more common with steel rope, while synthetic ropes may display fraying or fuzziness. Pay special attention to the terminations and splices. If you see anything suspicious—like significant wear on the rope’s core—it’s time to think about repair or crane wire rope replacement. Remember, consistent checks act as your first line of defence against unexpected failures later on.
Cleaning and Drying Techniques
Proper cleaning is crucial. For steel wire ropes, use a stiff-bristled brush or a recommended cleaning solution to remove grease, mud, or other residues that can harbour moisture. Synthetic ropes can often be soaked in a mild detergent bath, but be sure to read the manufacturer’s guidelines first. After cleaning, let them dry thoroughly in a well-ventilated area. Storing even slightly damp ropes raises the risk of mould, mildew, or corrosion, which can lead to costly replacements and downtime.
Labelling, Marking, and Organising
Finally, label and organise ropes according to length, diameter, or usage. Some worksites enlist colour-coded tags or tape to signal load rating or department ownership. By keeping everything marked, you’ll avoid the confusion of mixing ropes for different applications. Labelled cables also make it simpler to track usage patterns for each rope, which is a huge help when deciding on future rope installation or scheduling a crane wire rope replacement. Clear organisation goes a long way toward supporting wire rope safety and preventing mishaps.
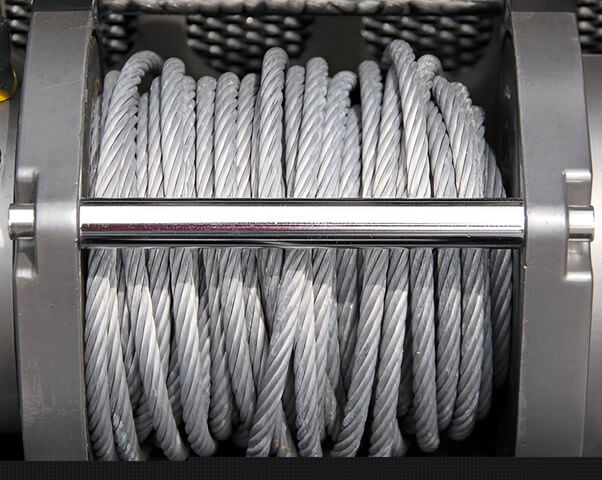
Best Practices for Long-Term Maintenance-
Long-term maintenance is more than a one-off task; it’s a series of ongoing actions that keep your ropes in the best possible condition. Whether you’re managing rope installation or connecting wire rope in a crane setup, consistent upkeep reduces the risk of accidents and unplanned downtime.
Proper Handling and Rope Installation Tips
Handling cable hauling ropes starts with the right technique. Never drag them across abrasive surfaces, and steer clear of forcing them around tight corners. Instead, use rollers or sheaves wherever possible. During rope installation, keep an eye on tension, ensuring it’s distributed evenly along the entire length. Over-tensioning can lead to internal damage that may not show up until you’re in the middle of a critical lift. Investing time in correct handling is worth its weight in gold.
Connecting Wire Rope Safely
Connecting wire rope is a routine part of many operations, whether it’s for crane work, cable logging, or tower construction. Always use fittings that match the rope’s diameter and load rating. Shackles, clips, and sockets should be inspected for wear, corrosion, or distortion before you trust them with any weight. A mismatch in size or a damaged connector is a recipe for disaster, especially under high stress. Make sure that connections are tightened according to the manufacturer’s specifications for maximum security.
Crane Wire Rope Replacement: When and How
Crane wire rope replacement becomes necessary when ropes exhibit significant wear, broken strands, or distortions. Pay particular attention to bends, kinks, or signs of flattening—these are red flags that immediate action is required. Replacing rope on a wire rope crane is a careful process: remove tension from the old rope first, feed the new rope gradually, and maintain proper tension throughout the installation. Regular lubrication helps the new rope last longer and protects the crane’s drum or sheave from undue friction. Scheduling replacements before a rope fully fails is a smart move that boosts safety and lowers potential downtime in the long run.
Conclusion
Storing cable hauling ropes correctly means more than just leaving them in a box until the next job. It involves careful inspection, periodic cleaning, and thoughtful organisation that supports both performance and safety. By reading through these best practices, you’ll be better equipped to protect your investment in ropes—whether you’re managing crane wire rope replacement or operating cable logging machines in the field.
Ultimately, the bottom line is that preparation and maintenance pay off in a big way. From simple tasks like labelling and drying ropes thoroughly, to more involved procedures like seizing wire rope ends for added security, each step contributes to longer-lasting rope performance. When storage is done right, you’ll experience fewer incidents and spend less on replacements over time.