Is your bulk material handling system operating at its peak efficiency? Are you ensuring that your equipment is properly inspected and maintained to prevent potential hazards and costly downtime? This comprehensive guide to bulk material handling inspection will help you maintain your system and keep it running smoothly, safely, and efficiently. We will discuss the importance of regular inspections, various inspection techniques, and common issues that need to be addressed during these evaluations. Start improving your bulk material handling process today by following this in-depth guide.
Key Components and Systems to Inspect-
A thorough bulk material handling inspection should cover all major systems and components within your facility, including:
Conveyor Belts and Accessories-
Inspect conveyor belts for damage, wear, and alignment. Review belt tension and tracking to ensure proper operation. Evaluate belt scrapers, belt cleaners, and other belt maintenance accessories to ensure efficiency.
Conveyor Rollers and Idlers-
Evaluate conveyor rollers and idlers for proper alignment, lubrication, and wear, ensuring that they are free from debris and properly functioning.
Conveyor Pulleys and Bearings-
Inspect conveyor drive, tail, and snub pulleys for wear, alignment, and lubrication. Assess bearings, bushings, and sprockets for signs of wear or failure, ensuring proper alignment and lubrication.
Dust Collection Systems-
Review dust collection systems for leaks, blockages, and proper filter functionality, minimizing environmental and health impacts.
Chutes and Loading Equipment-
Evaluate chutes, hoppers, and other loading equipment for build-up or spillage, ensuring proper material flow and reducing potential hazards.
Silos, Bins, and Storage Facilities-
Inspect silos, bins, and other storage facilities for leaks, corrosion, or material build-up, verifying proper flow and preventing potential hazards.
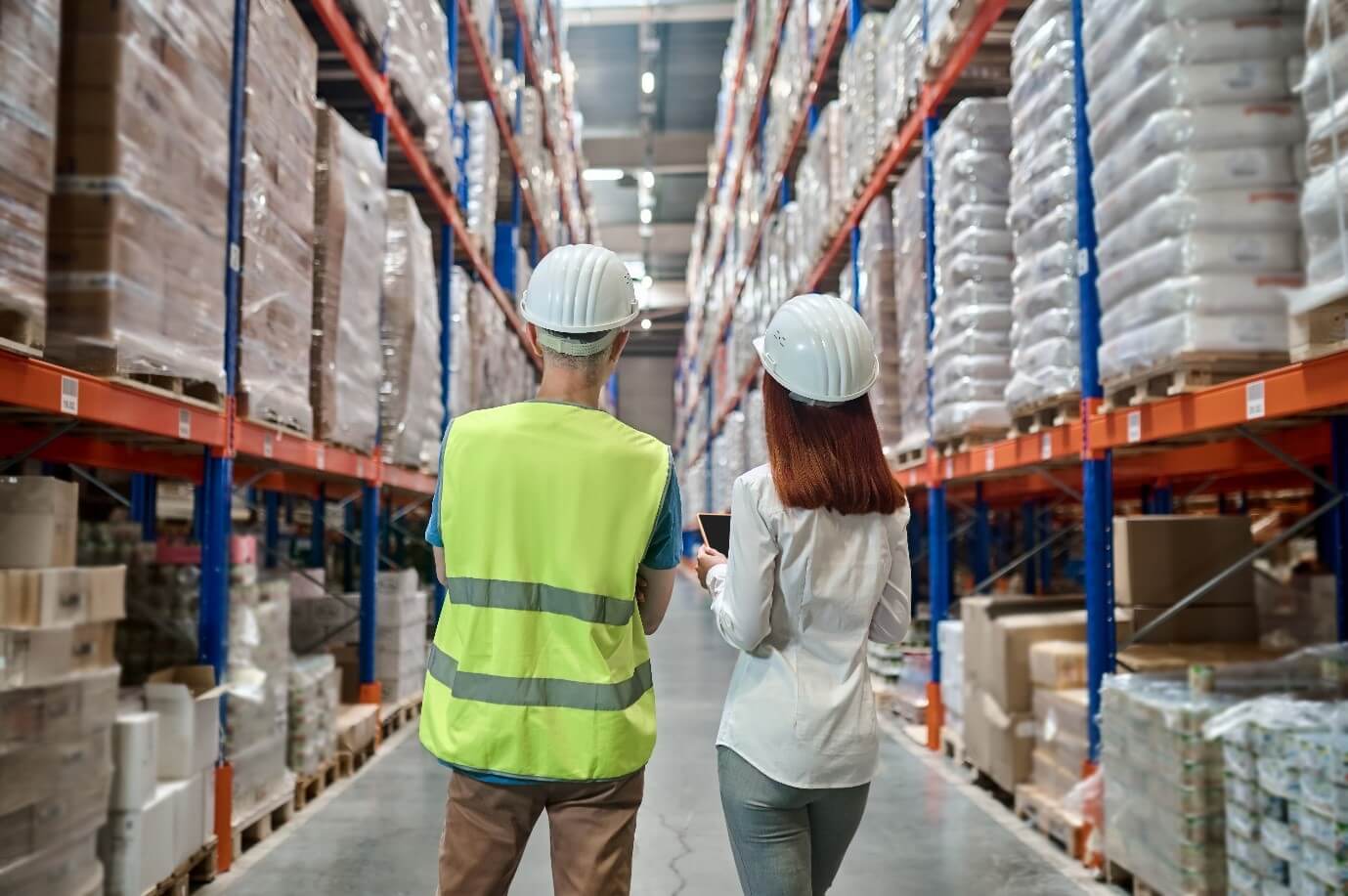
Inspection Techniques and Tools-
Incorporate various inspection techniques and tools to ensure a comprehensive evaluation of your bulk material handling system, such as:
Visual Inspection-
Observe the physical condition of equipment and systems, looking for signs of wear or damage, belt mistracking, and material buildup.
Vibration Analysis-
Monitor vibration in your machinery to detect component wear, misalignment, and lubrication issues early on.
Infrared Thermography-
Utilize infrared thermography to analyze temperatures in your machinery and detect damaged parts, misalignment, or poor lubrication.
Ultrasonic Testing-
Employ ultrasonic testing to assess thickness and integrity in metal and non-metal components, detecting wear and potential failures early on.
Non-destructive Testing (NDT)-
Use various NDT methods like radiography, magnetic particle inspection, and dye penetrant testing to identify cracks, flaws, and other defects without damaging equipment.
Common Issues Found During Inspections-
Be prepared to address common issues found during bulk material handling inspections, such as:
Conveyor Belt Mistracking-
Address alignment issues, pulley and roller wear, and other factors that contribute to belt mistracking.
Material Spillage-
Identify causes of material spillage, such as improperly designed chutes, worn belt scrapers, and inadequate sealing.
Dust Emissions-
Manage dust emissions by identifying leaks, ensuring proper dust collection system operation, and maintaining sealing and containment systems.
Equipment Wear and Damage-
Evaluate the condition of all components in your material handling system, scheduling regular replacements and upgrades as needed.
Developing a Comprehensive Inspection and Maintenance Plan-
Following a comprehensive inspection, develop a complete maintenance plan that outlines:
• Inspection frequency for each component or system
• Necessary maintenance tasks, such as lubrication, wear part replacement, and repairs
• Scheduled downtime for more extensive maintenance
• Contingency plans for unexpected equipment failures
The Role of Safety in Bulk Material Handling-
A thorough inspection plan and proper maintenance practices are essential for maintaining a safe working environment in your bulk material handling facility. Always abide by applicable regulations and guidelines to ensure the safety of your employees and the smooth operation of your business.
In conclusion, conducting regular bulk material handling inspections is a critical step in optimizing the efficiency and longevity of your system. By addressing common issues and implementing a comprehensive maintenance plan, you can ensure the safety of your employees, reduce downtime, and ultimately save money. Prioritize the inspection and maintenance of your material handling equipment today to ensure your system’s ongoing success.